
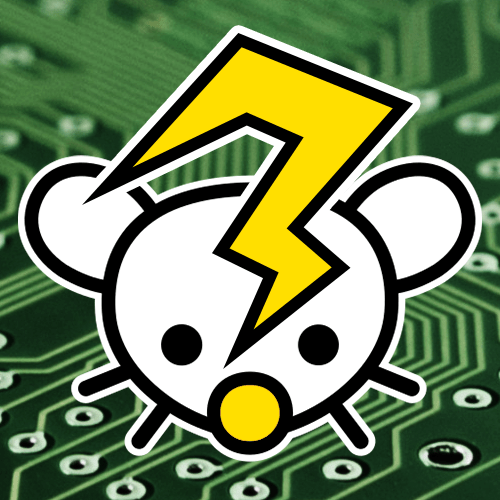
No worries! I appreciate that you were just trying to assist!
No worries! I appreciate that you were just trying to assist!
Battery University is indeed a great resource!
However this is not a lithium polymer battery, and as it’s a 32700, it is not a prismatic or pouch cell either. It is a lithium iron phosphate (LiFePO4) cylindrical battery in metal housing. Battery University does have them listed in their table of chemistries (in case you’re curious), but they don’t seem to have much detailed information. Enough to build a charger though :)
https://batteryuniversity.com/article/bu-216-summary-table-of-lithium-based-batteries
Also some more detailed information here:
https://batteryuniversity.com/article/bu-205-types-of-lithium-ion
Anyway, thanks for your reference in any case! I’m not responding to criticize you, only to improve the utility of this conversation in case someone else finds it on search :)
Makes sense!
I’d order online if there was a LiFePO4 charger on the market. However, in my country I’ve been unable to find one, and importing (excise & duties, paperwork) is more work than building it myself. I’ll also likely need a design that I can cheaply include on custom PCBs for manufacture (not for sale to end-users, but for internal use by maintenance technicians).
I gave it a test on a cell today and it seems to charge fine and at a reasonable rate – but in a sudden flash of brilliance, I forgot to physically connect the ADC pin to the battery, so it couldn’t shut off. Well, that’s what testing is for I guess.
Anyway after fixing this, it looks like I can call this a win and move on. If it undergoes destructive optimization, I’ll report back here with a warning to others.
No, that won’t work.
A vibration switch will work.
If that’s not sensitive enough, another option is using a piezo element coupled to the case to detect vibration, with an op-amp or hex inverter to buffer + trigger the 555. However if you couple it too closely with e.g. the floor or furniture it will pick up nearby footsteps or cars. Might be good depending on the situation.
That sounds even better!
Hm, that reminds me! If you’re designing your own PCB, some manufacturers will make the PCB out of aluminum for you instead of FR4. This is commonly used for high-intensity LED lights to help keep them cool.
Here’s some random info about them so you can see what I mean:
https://www.pcbgogo.com/Article/An_Introduction_to_Aluminum_PCBs_by_PCBGOGO.html
An alternative would be copper-clad polyimide adhered to the body. That also has better thermal properties than FR4.
In seconds? Wow. I think you’re right, you might need more than a small fan!
It might be worth exploring heat pipes or peltier effect coolers. The latter makes the problem worse (they are inefficient and generate a lot of heat) but your LED can be locally cooler if you can e.g. move all that extra heat into a big heatsink (also condensation can be problematic).
One cheap source of heat pipes for testing could be old graphics cards – they often outperform simple copper heat sinks. Use thermal epoxy to stick your LED to it and see if the performance is acceptable. On the exotic end of things, you could also water/oil cool it, or (carefully) make your own thermal grease from industrial diamond powder for a small boost in thermal conductivity.
Also even at 95% efficiency, it sounds like your boost converter has some heat to dump too!
Hah! I totally didn’t notice that. Good catch.
These are the smallest fans that I know of: https://www.mouser.com/new/sunon/sunon-mighty-mini-fan/
They go down to 9mm x 9mm x 3mm.
If this is to cool some component in the flashlight, have you considered a heatsink instead?
Yup, seen that for sure.
Did you try turning the little adjustment knob in your probe to calibrate it? Sometimes needs a small screwdriver. Here's a reference:
https://www.elecrow.com/download/HowToCalibrate10xProbe.pdf
What I'm referring to is labelled 'Cap Trimmer'. The document also has some waveform images that match your problem.
I have a Siglent and it looked like this at the dealership, then they adjusted the probe a bit, and then it was 100% fine.
Glad to help :)
Besides the I/O and supporting hardware, the clock speed is wildly different between these 3 chips – that's worth considering. By that metric, the ATMEGA based designs are the slowest by far – although somewhat faster than you'd estimate since they usually operate 1 instruction per clock cycle, whereas the other chips are a few clock cycles per instruction (they are still way faster than the ATMEGA line though).
Regarding pre-made boards vs. your own? I think there are three things to consider:
Pre-made boards are awesome for prototyping. Making sure the damn thing will work (feature-complete) before designing your own board is a good idea. Then, make your first board with all features added in (this is important), but expect to iterate at least once (make revisions and order boards a second time). There's no such thing as premature optimization in hardware design – it's not like software where you can just design the core of an application and then build features as you go. This is why always designing prototypes to be feature-complete is a good workflow, and generic development boards are a good starting point for this.
Designing your own board is really easy for AVRs. I do this all the time, lately with the Attiny10. Honestly there are a ton of AVR chips out there, and not all of them have affordable / popular development boards, so often it's worth making your own for use in item 1 above (…really you just need at minimum power and a header to break out the pins for ISP programming). Then when you want to make your final widget, you just expand your development board design, which lets you make a really miniaturized and streamlined thing! You will need an ISP programmer though, like the AVR-ICE (which has a nasty but minor bug in the design – ping me before buying one and I'll save you 2 days of headaches setting up).
A neat trick is to design your own boards and still use a dev board (so making your own boards and buying premade dev boards are not mutually exclusive options). This is especially useful with the Pi Pico and ESP32 (where making a dev board is less beginner-friendly) – a cheatcode is "castellated mounting holes". These let you solder (for example) a Pi Pico dev board directly to your own design as a surface-mount component. You can do this by just adding a socket and using header pins too, but SMT + castellated mounting holes lets you keep the design small and reliable.
BTW when designing your own boards, committing to SMT parts (where possible) early on is one of the things I'm really glad I did. You don't need much tooling to do it. Just a solder paste syringe, a toothpick or pin, some tweezers, and a hot air rework station (included in some soldering stations). Even 0402 parts (about the size of two grains of salt) are pretty easy to do by hand. It's amazing the level of miniaturization that you can achieve these days this way, as a private individual with a very modest budget!
Finally, the Arduino products are generally very good dev boards, whether or not you're using the Arduino IDE (you can still program them ASM or non-Arduino C++). So for any chip that an Arduino exists for, it's an excellent starting point – although you may want to design your own board one day to remove unnecessary stuff if it comes out cheaper and you go through a lot of them, or just for the experience.
There are a lot of differences, but I'll try and go over the high level ones. The RP2040 is a chip, and the others are boards – so I'll compare the chips on them.
The RP2040 chip is really powerful overall, and does some odd things with I/O that let you do a bunch of very fast, precise things. You also get a lot of I/O pins and they are very well-behaved. The main advantage though is that it works well in both Python and C++, and is well-supported.
The ESP32 based board (Thing Plus) has integrated WiFi. The ESP32 is a great chip, I use it a lot, but it has some unfortunate quirks. First, it has a very high clock speed and decent memory, making it quite powerful. However, if you glitch out the network stack via your code, it can have some problems with unexpected resets. This was much worse with the earlier-generation ESP8266. Secondly, the I/O work much more slowly than the system clock (if I recall correctly), and they are picky about what state they have on startup – some go high as part of the boot process, others must be high or low on boot but can be used after. This is actually quite a pain sometimes. It's a great chip overall though and works well in C++.
The Pro Micro uses an ATMEGA32 chip. I'm a huge AVR fan so I don't have many bad things to say, I like it a lot. It is much slower than the other two chips though, and has less memory. Probably it's best to use C++, but you ought to be able to use Assembly too if you like. The I/O on AVRs are really well-behaved and usually operate at the same speed as the chip, which is nice when you need precise timing! The best thing about it though, is it can use much less power than the other two options, if you use the sleep modes right. So you can build neat battery-powered applications. Finally AVRs have excellent datasheets – there's rarely any ambiguity on exactly how any system on the chip works.
Overall, I'd choose an RP2040 board if I wanted to use Python and do IoT/Robots/whatever (you can buy boards with or without WiFi), an ESP32 based board if I wanted to do IoT stuff in C++, and the Pro Micro if I wanted to do low-level, low power embedded stuff in C++ or assembly (and maybe branch out into other AVR chips). The C++ options mean you can use the Arduino IDE and their libraries.
The most important thing is to tackle projects frequently and get yourself involved with other people doing the same. Learn by doing! I found books, videos, and so on of limited utility by comparison. I'll include an unreasonable quantity of my notes below.
Some useful resources:
List of initial things to learn:
How to read component datasheets (you will be doing this a lot). Actually I think a lot of my electronics knowledge was picked up from just absorbing datasheets like a weird sponge of some sort.
How to order from Mouser / Digikey / RS Components / Arrow / McMaster (these are also a great source of datasheets)
Basic laws of electricity and magnetism (any freshman university physics textbook is OK – these pop up used all the time, and even an old one is OK). Just do all the problems in each chapter and you'll be fine. Or you can tackle "The Art of Electronics" if you like.
If you're into analog, this is a classic (and free!) text : https://web.mit.edu/6.101/www/reference/op_amps_everyone.pdf
Soldering is actually pretty easy, just buy some resistors and some prototyping board and get some practice in. You'll need to learn surface mount soldering to get access to good and cheap parts later on, but thankfully, it is way easier than it looks. Like, really a lot easier than people make it look.
How to order manufactured circuit boards from a factory using a design in KiCAD (this is actually pretty easy and cheap!)
These days, a lot of components can be purchased on pre-built 'modules' that fufill a certain objective. For example, a temperator sensing module might have a sensor and all the supporting components on a little board, so you just connect power+ground and data. These are made specifically with learning in mind and are made in Asia at a very reasonable price – do note though that reading the actual datasheet of the parts in question will give you much deeper knowledge over time.
Tools to buy:
Platforms and Communities to Consider:
Other Stuff:
Ping me if you get stuck or have questions :)
Good advice all around! Thanks!
I’ve also messed around with the ESP8266 and various models of ESP32. Their WiFi time-of-flight stuff is interesting. I’ve quite a few projects with both actually! My main complaint is that the GPIO don’t behave nicely (also the esp8266 is a power hog and reboots if you screw up the network stack). They are much slower than I’d expect, and have weird states on boot. It’s not too bad to work around this stuff, but I chose the Pi Pico W so as not to have to explain it.
It still blows me away that I can easily do public-private key encryption on the ESP32. And graphics. At the same time!
Haha, I know exactly what you mean – I’m most interested in resource-constrained embedded systems. I like the attiny10 a lot. At work I mostly write Python, but in my own time it’s mostly assembly language. It feels more concrete, every decision matters, and anything that goes wrong is 100% your fault as there are relatively few bugs at that level. It’s a lot of fun. Also the datasheet is very good.
I’m self-taught with all the electronics stuff, I paid for it by teaching a course on whatever thing I did most recently. Then I’d use the proceeds to buy tools and parts for the next big (often dumb) idea. I’d also ask for the software engineering assignments from colleagues in those programs, and complete them in my spare time. It was puzzling to a few people why I would want to do assignments, and indeed some were very boring (oh god Java + Spring framework) but others were quite interesting (formal study of algorithms). Sadly, economic reality kicked in and I had to run a company instead of pursuing my education further (I still try to do one ridiculous engineering thing per year though).
I guess there’s a real risk (…like 100%) that I overestimate the motivation students have – so I think I’m going to take your advice and set the level of abstraction with something API-like to abstract away the low-level components (this is closer to my client’s domain). I’m imagining a robot that acts as a WiFi access point, and having something “like an API” that works over UDP packets that describe high-level functions. Then start with something simple – like a digital map with known starting location, and a small obstacle course that can be completed with simple distance measurement, no point clouds. If that goes well, I can develop towards more complex material – probably not full SLAM, but maybe localization on a pre-mapped surface. I have plenty of my own code as examples of how to do simple UDP communications in Python, I could expand it into a custom library.
Sort of like Logo from 1983, but with a physical robot and sensors. I’m a little to young to have used Logo, but the computer lab in my school was really outdated so I got to try it once :D
Yup. Agree. Probably going to go with a LiDAR-first approach.
They’re university software engineering students, probably a year or two into their degrees. I’m hoping to provide the robots as completed units that are controlled via API, because we’re not likely to get many students with electrical, mechanical, or embedded backgrounds. You’re right about the complexity though, and that’s something I’ve been thinking about – I guess I’ll start out with a bit of optimism regarding their talents, and scale back if needed :D
I don’t really have a scope, budget, timeline, or audience properly defined for this project – in short my client has a STEM program for building and interacting with digital maps, but it’s way too boring and I’m determined to breathe some life into it. So I’m going to have to play a lot of things by ear.
Ok yeah – I’m leaning toward relying more on the laser ToF than the rotary encoders.
A simple algorithm of ‘pick a lidar point and drive toward it’ does sound simplest. Thanks for weighing in!
Glad to help! I find it quite neat that with effort and time, it’s possible to learn to make quite advanced electronic systems yourself at home. Some of the stuff the more advanced hobbyists make is quite a bit better than a lot of mass-produced goods. We truly live in an age of wonders!
An international parts order is too complex for such a small thing. I’m not in the USA or China. So no TP5000 for me, got to work with what I have.
I agree, no charging at 4.2 volts. The current charger I built seems to work well enough. I ran some tests and it charges within spec. The reason I turn off the charger to measure cell voltage is because otherwise I’ll mainly be measuring SMPS noise.
Anyway it beats the charger available in the local market, which is clearly unsafe, no matter how much they assure me that it’s ‘totally OK’.